The new concrete flooring system that won’t end up in landfill
Pictured above: Grant Brown and Andrew Minturn.
Two Auckland entrepreneurs have invested millions of dollars over 10 years developing a building product that is effectively invisible. And that’s got some big names in construction excited.
Clevaco co-founders Andrew Minturn and Grant Brown say while no magic is involved, they have come up with a circular solution to a major waste issue in construction and demolition.
In simple terms, their product reduces the amount of concrete needed for concrete slab floors. While that’s not a new concept, they are changing the game with a material that can make building more sustainable.
For the past 30 years, builders here and in Australia have used polystyrene blocks as space savers in their concrete floors. Concrete is poured between and over the blocks to form the foundations. The blocks reduce the volume of concrete needed for a job, reducing costs and embodied emissions. In the building industry this type of concrete foundation is known as a waffle pod floor or RibRaft (Firth Concrete).
Great idea but there are some downsides. Polystyrene is messy to work with and the poly beads contaminate the environment. Concrete also bonds to the polystyrene blocks like glue. This causes problems years later when the floor is demolished. The polystyrene can’t be separated cleanly from the broken-up concrete and reinforcing steel. Instead of being recycled, those valuable materials are dumped in landfill.
Andrew describes that as an “environmental catastrophe that our children and grandchildren are going to have to deal with”.
He estimates the foundations of an average-sized house would produce about 40 tonnes of contaminated concrete when demolished.
“To put that into perspective when all the concrete floors with polystyrene that have been built here in the last 30 years are demolished, the volume of waste being sent to landfill will be equivalent to nine Giza pyramids.”
Enter Clevaco with its Cleva Pod system. Made from recycled and waste plastic, the pods work just like polystyrene blocks but without creating waste during installation or demolition. The pods are easy to cut to size, if necessary, and the plastic can be retrieved when the floor is demolished. Left over pods can be reused, while damaged pods and installation offcuts can be recycled a minimum of three times.
Recycling concrete and steel reinforcing saves money on landfill costs that are increasing every year. In 2024 it cost $588 to dump one tonne of contaminated concrete construction waste in landfill. Recycling also reduces the need for new concrete and steel to be made. This helps reduce emissions.
The Cleva Pod system helps reduce emissions in other ways. The standard pods measure 1.1 metres square and stand 22 centimetres high. They are easy to stack for delivery and lightweight which helps reduce transport emissions.
Andrew says the Cleva Pod system provides a like-for-like alternative to polystyrene.
“The only difference, other than the ability for re-use, is the price and we’re trying to keep that down as low as possible. While you pay a bit more upfront you end up saving huge amounts at the other end. A life cycle analysis of a house slab foundation shows our system can save $40,000 to $50,000 in demolition, cartage and dumping fees.”
Cleva Pod was officially launched late last year.
Andrew admits the timing wasn’t great due to the slow down in the construction sector both here and in Australia, caused by tough economic times.
However, there has been an encouraging response. The business was awarded an ASB Backing Business Grant in 2021 and won the 2024 Tāmaki Makaurau Zero Waste Innovation Award for the Cleva Pod system.
Andrew and Grant are now talking with two large players in the construction industry interested in their product.
“They’re very seriously considering moving over to more sustainable products like Cleva Pod. If we get one of those major players it will validate all the work we’ve done so far,” says Andrew.
That work started 10 years ago for Andrew and business partner Grant, operating out of a garage. While the basic idea of finding an alternative to polystyrene seems simple, it has proved challenging.
The design has been through many iterations. They’ve worked closely with Australian injection moulding company Socobell as no company in Aotearoa New Zealand has equipment large enough.
Related: Nailing sustainable design
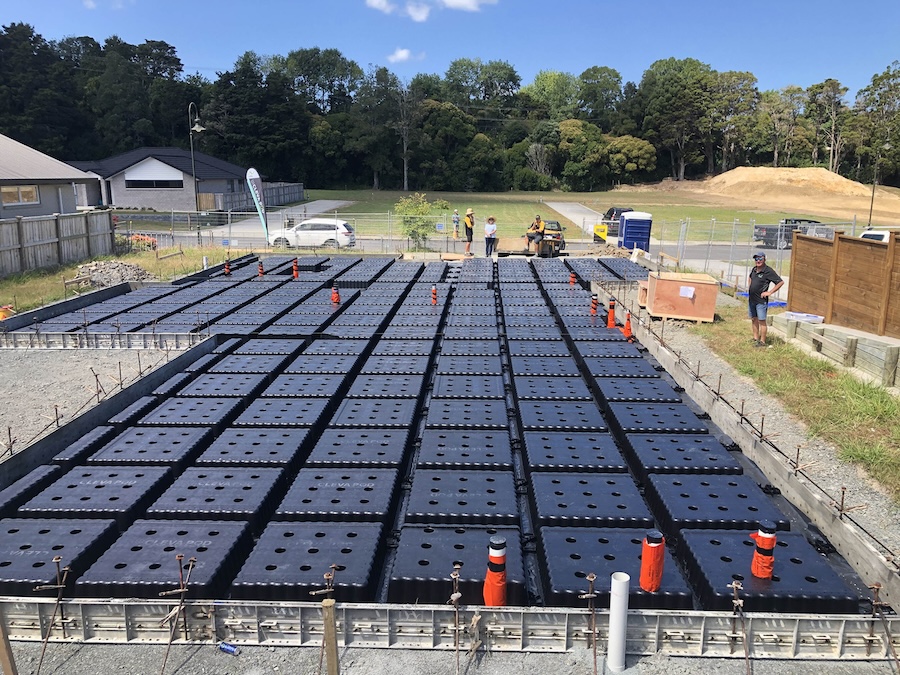
“We reckon we’ve invested between $5-6 million dollars over the past decade. That includes all the designs, moulds, testing, patents and trademarks.
“We have an incredibly strong belief in what we’re doing from a product and design point of view. Plus the positive feedback we’re getting from the sector is really encouraging.”
Andrew says changing expectations and regulations are also driving interest in Cleva Pod.
“Companies are starting to acknowledge and sometimes sign up to protocols, be it national or international, on sustainability and resource recovery and carbon reduction. And you can’t achieve any of those with polystyrene.”
Firth Concrete provides a technical manual for engineers designing RibRaft floors. It includes the Cleva Pod system as a more sustainable alternative to polystyrene.
Clevaco is part of the Sustainable Business Network and is included in its Next 95 list of innovators and visionaries.